Concord Biotech announcement for walk in interview on 15 February 2025 for multiple position in pharmaceutical sector. Concord Biotech limited conducted walking interview on various position in Quality insurance, Quality control and Microbiology at Ahmedabad location.
Here’s a section with interview Answers and Questions that we can added in this blog post to help candidate prepare for interview at Concord Biotech or any other company.
Table Of Contents |
---|
1. Company Profile |
2. Vacancy Details |
3. Walk-In interview Details |
4. Mandatory Documents |
5. Interview tips and trick |
1. CONCORD BIOTECH Company profile :
Concord Biotech limited is a R&D driven biopharma company that manufacturers active pharmaceutical ingredients (API) through fermentation and semi synthetic process and finished formulations.
Concord Biotech limited founded in year 2000 has transferred from a single product company to a board spectrum solution provider, offering products across diversified therapeutical segments.
Concord is globally knows for its products and has a commanding presence in more than 70 countries worldwide.
Concord manufacturers and supplier nephrology and critical care range of finished products to global markets.
2. CONCORD BIOTECH Vacancy Details :
Vacancy No : 01 | |
---|---|
Department | Quality Control |
Position | Officer / Senior Officer |
Qualification | B.sc / M.sc / B.pharm |
Experience | 2 to 8 years of experience in QC Analyst. |
Vacancy No : 02 | |
---|---|
Department | QC – Microbiology |
Position | Officer / Senior Officer |
Qualification | B.sc / M.sc in microbiology |
Experience | 2 to 4 years of experience in OSD facility as a Microbiologist. |
Vacancy No : 03 | |
---|---|
Department | IPQA |
Position | Executive/ Officer / Senior Officer |
Qualification | Msc. / B.pharm |
Experience | 5 to 8 years of experience in IPQA with OSD facility. 5 to 8 years of experience in analytical raw data review. |
3. CONCORD BIOTECH Walk-in Interview Details :
◾ Interview Date : 15th February 2025
◾ Interview Time : 9:30 am to 3:00 pm
◾ Interview Location : Concord Biotech limited, B1601-1602, B- Wings, Mondeal Height, Iscon cross road, S.G Highway, Ahmedabad
◾ those who are unable to attend interview can share cv on careerfdf@concordbiotech.com with mentioned position Applied For in subject line.
4. Mandatory Documents :
- Updated Resume
- Current Salary Proof
- Education Proof
- One Photograph
- Experience Documents
5. Interview tips and trick :
1. Tell about your experience in quality control ?
Ans : highlight your experience in various QC activities such as inspection, testing, process control, and using QC tools. Be specific about the industries you’ve worked in and any key projects you’ve are handled.
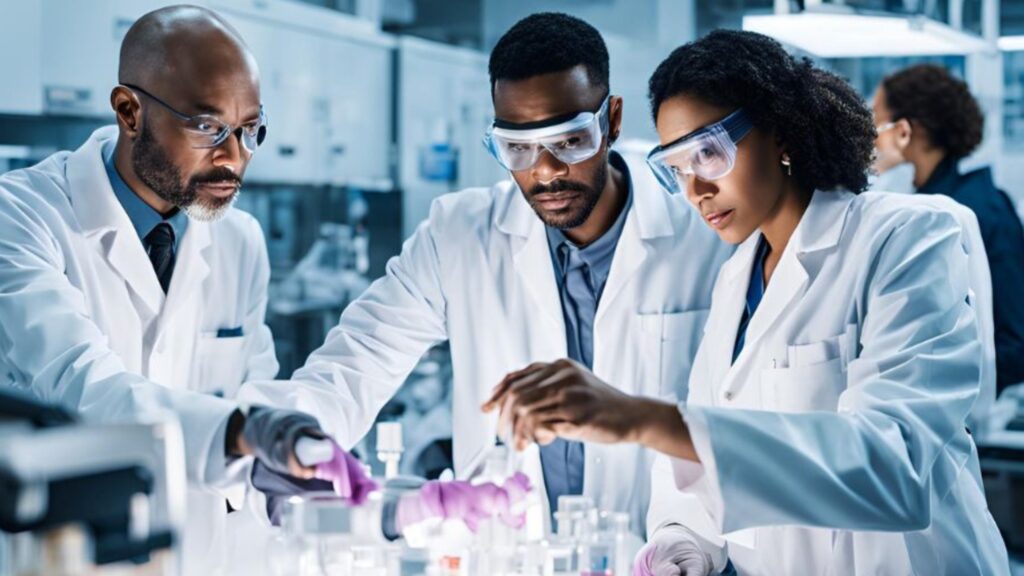
2. What is the different between Quality control and Quality assurance ?
Ans : Quality Control (QC) focus on detecting defects in the final product through inspections and tests. Quality assurance (QA) is the proactive process of preventing defect by improving and managing the processes that lead to product development.
3. What are the various type of quality control techniques ?
Ans : Common QC techniques included as per below:
▪️Inspection : Visual or physical checks for defects. ▪️Testing :verify product performance ( example functional stress or security testing ). ▪️Statistical process control : monitoring and controlling the process through statistical method. ▪️Six sigma : a data drive approach for improving quality and reducing defects. ▪️Pareto analysis : identify the most significant problems by sorting defects by frequency.
4. What is a Control chart ?
Ans : A control chart is a graphical representation of a process over time. it shows the performance of a process and highlights any variations that may require attention. it helps in monitoring the stability of a process and determining if it’s in a state of statistical control.
5. What is the role of quality control inspector?
Ans : A QC inspector is responsible for examining products or materials to ensure they meet predefined quality standards. They perform taste, inspector, products document findings and collaborate with production terms to resolve quality issues.
6. What is the purpose of an inspection plan ?
Ans : An inspection plan outlines the quality control activities to be performed during the production process. It defines the specific tests frequencies, criteria, and standards for inspection to ensure products meet quality specifications.
7. What tools do you use for quality control ?
Ans : QC tools include :
▪️Check seats for data collection. ▪️ Histograms for visualizing data distribution.▪️ Flow charts to make out processes. ▪️ Scatter diagrams for analysing relationship between variables. ▪️ Control charts for process monitoring.
8. What is the process of calibration in QC ?
Ans : Calibration ensures that measuring instruments provide accurate and consistent results. the process involve comparing the measurement tool against a know standard, making adjustments it necessary and documenting the calibration for traceability.
9. How do you handle non- conformance ?
Ans : Non-conformance is when a product or process does not meet specified requirements. the process for handling non conformance typically included : ▪️ identifying and documenting the issue.▪️ Investigating the cause (root course analysis). ▪️Implementing corrective action ( fix the issue) ▪️ Reviewing the process to prevent recurrence.▪️communicating with stakeholders about the resolution.
10. Can you describe your experience in IPQA?
Ans : In my 8 year experience in IPQA, I have been responsible for ensuring that all processes during manufacturing comply with the required quality standards. I’ve managed batch documentation, conducted in process checks verified equipments calibration and performed sampling checks. I also collaborated with the production team to troubleshoot issues and provided regular feedback to maintain product quality.
11. How do you ensure that all in process checks are performed according to the required standards?
Ans : I ensure that all in process checks are conducted as per sop and guidelines. I regularly review batch records make sure that process parameters are met and maintain communication with production terms to address any deviations immediately. I also ensure that corrective action are implemented and documented as part of the continuous improvement process.
12. How do you handle deviations in the production process ?
Ans : When I notice a deviation in the production process, I first investigate the root cause reviewing batch records and inspecting the equipment involved. I then report the deviation according to our protocol ensure immediate collective action is taken and work with the production and quality control teams to implement a preventive measures. documentation is key, so I ensure everything is recorded for audit and compliance purposes.
13. How do you handle situations where the production team does not follow IPQA procedures ?
Ans : In such situations I address the issue promptly by discussing it directly with the production team to understand why the procedure was not follow. I provide guideline and training if necessary ensuring they understand the importance of procedure for product quality and regulatory compliance. if required I escalate the issue to my supervisor to ensure corrective actions are in the place.
14.How do you stay updated with regulatory changes and industry standards ?
Ans : I regularly attend webinars, industry conferences and training sessions to stay updated on the latest regulatory changes and industry best practices. I also subscribe to industry publications and maintain a network with other quality professionals. I ensured that any relevant changes in regulations are communicated to my team and incorporate into over processes.
15. What quality tools or methodologies are you familiar with and how do you apply them in IPQA?
Ans : I am familiar with various quality management tools such as FMEA (failure mode and effect analysis) CAPA (corrective and preventive action) and root course analysis. I apply these tools to identify potential risks in the production process investigate deviation and implement and preventing measures to ensure product quality. I also utilize trend analysis and statistical process control to monitor process stability.
If you Required more questions and answers please comment…Thank you for Reading
Important Link :
Latest Job Update 2025 : Click Here